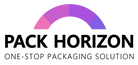

NEWS
EN ES FR DE IT
Time: 2024-02-05
Comparison Between Glass Frosting and Sandblasting

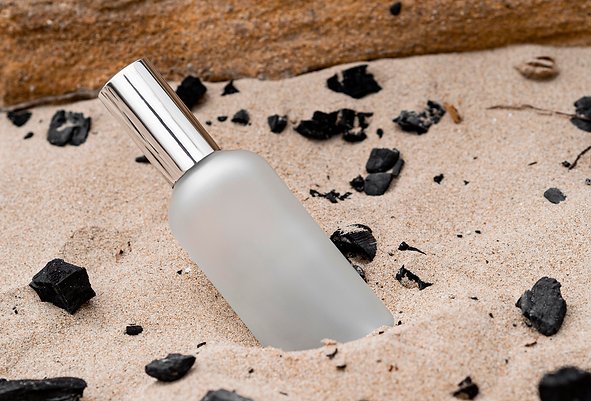
Table of contents
-
Sandblasting introduction
-
Frosting introduction
-
Frosting Process
-
Sandblasting Technique
Sandblasting Introduction
Sandblasting is a process that uses compressed air to propel abrasives onto the surface of a workpiece for treatment. This is known as sandblasting or shot peening. Early in the shot peening process, sand was the only available abrasive, so sandblasting became the term used for this type of treatment for a long period. Sandblasting can clean surfaces to the required level and create a specific roughness, which also improves the adhesion of coatings to the base surface. Regardless of the quality of the coating, if the surface is not properly treated over a long period, the coating will not adhere properly. The goal of surface pre-treatment is to clean the surface and create the roughness necessary to "lock" the coating to the surface. After sandblasting, if a high-performance industrial coating is applied, the coating's lifespan will be 3.5 times longer than coatings on surfaces treated by other methods with equal quality coatings. Another advantage of sandblasting (shot peening) is that the surface roughness can be predetermined and achieved during the cleaning process.


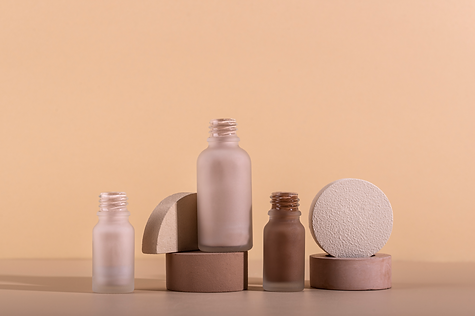
Frosting Introduction
Frosting is a process where the smooth surface of a glass cosmetic bottle is made rough, causing diffuse reflection of light. In chemical frosting, glass is ground or hand-ground using abrasives such as diamond dust, silica sand, garnet powder, and other materials to form an evenly rough surface. Alternatively, glass and other objects can be treated with hydrofluoric acid to create frosted glass.
Both frosting and sandblasting are used to obscure the glass surface, so that when light passes through a lampshade, it creates a relatively uniform scattering. Ordinary users find it difficult to distinguish between the two techniques.
Below are descriptions of the manufacturing processes and how to identify them.

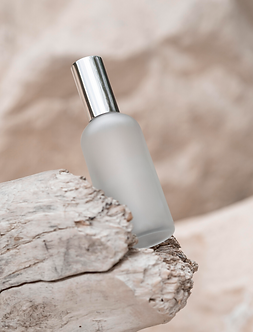
1. Frosting Process
Frosting involves immersing glass in a prepared acidic liquid (or applying an acidic paste) to corrode the glass surface with strong acid. The hydrofluoric acid in the solution causes crystals to form on the surface. If the frosting process is done well, the frosted glass surface is very smooth, and the crystals formed by the scattering produce a hazy effect. If the surface is relatively rough, it indicates that the acid is aggressively corroding the glass, or some areas have not yet formed crystals. The characteristic of this process is the appearance of shiny crystals on the glass surface under critical conditions. The main reason for this is that the hydrofluoric acid has almost been consumed. To reach this state, many manufacturers have conducted numerous attempts and research but have not been able to overcome this challenge.
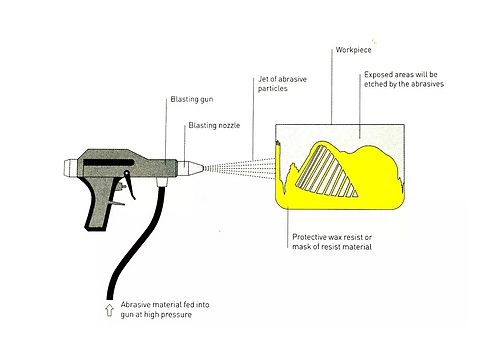
2. Sandblasting Technique
Sandblasting uses a sandblaster to shoot high-speed sand particles onto the glass surface, creating a fine rough surface that achieves the effect of light scattering, giving the glass a hazy appearance. Glass products made with sandblasting have a rough tactile feel. Since the glass surface is damaged, it appears white in comparison to the original transparent glass due to its light sensitivity.
These two processes are completely different. Frosted glass is more expensive than sandblasted glass, and the choice depends mainly on user needs. Some unique glasses are not suitable for frosting. From a refined perspective, frosting should be chosen. Sandblasting can be performed in general factories, but frosting is more challenging to execute properly.
Surface Treatment Techniques